EKF5
Active Member
Several threads have been devoted to providing a definitive catalog of keys to the TARDIS. After reading them and going back to some of them an extra time or two I decided that I needed to have a TARDIS key. I like the fan keys much more than the standard keys and thought I'd make one.
I looked at the great reference photos in the threads and decided that I don't like the Rassilon seal as much as I like the new Time Lord seal so I decided to make a fan key with the Time Lord Seal (drawn by Peter McKinstry) in place of Rassilon's. This is the coaster with the seal on it made by Rubbertoe Replicas. That's the design that will go in place of the seal of Rassilon.
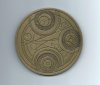
I'm far enough along with this that it's a project instead of a wish and over the next day or two I'll post some pictures of my design, approach, and progress.
I looked at the great reference photos in the threads and decided that I don't like the Rassilon seal as much as I like the new Time Lord seal so I decided to make a fan key with the Time Lord Seal (drawn by Peter McKinstry) in place of Rassilon's. This is the coaster with the seal on it made by Rubbertoe Replicas. That's the design that will go in place of the seal of Rassilon.
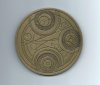
I'm far enough along with this that it's a project instead of a wish and over the next day or two I'll post some pictures of my design, approach, and progress.