Moska
Sr Member
Hello friends.
I present my new model. A work that began as a restoration project but, due to the poor state of my old model and the inaccuracy of the kit, finally became a construction project almost from scratch.
• Rescued Pieces:
I Rescued a few pieces of my old model (built in 1995) which was already spoiled by having been exhibited without protection for many years.
From that model I only rescued the cockpit with its pilots and the rear radiator.
The cockpit that I built is very rich in details regarding the kit piece, and the pilots are the pieces provided by the kit, but I remove their heads to leave empty helmets and filled these spaces with new and better modeled heads. I also put their corresponding goggles from a transparent yellow acetate sheet.
The only update after 20 years was to add a plastic strip in both helmets, in the relief that runs along the upper central line. The original relief of the pieces is very flat and needed more height to become more like the real helmets. Aside from that, I didn't need to re-touch up the paint job done so long ago. The cockpit had been well protected behind the glass of the windows.
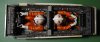
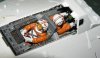
The rear radiator was also very well preserved because it had been painted with Humbrol polished metal, and not appreciated in its finish any alteration. This piece is the one that comes in the AMT/ERTL kit without any transformation or improvement.
• Parts from a new kit:
Almost all parts that I used from the new kit had to be worked to match the original model. The only parts that I used from de box are the supports of the lower airbrakes.
- Fuselage: First I removed completely all panel lines and details in relief, and then I go back to carving all the new lines and adding the small reliefs with different thicknesses plastic sheet.
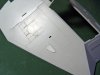
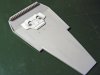
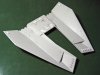
I cut the front grid into rectangle shape by the process of repeatedly passing the edge of a blade to make the cut as thin as possible. Once the rectangle was removed, I sanded the rest of the grid that remains in the main part of the fuselage until it disappears, leaving the front surface completely smooth. Then I pasted the rectangular piece in place, but leaving it a little swamped with respect to the surface that surrounds it.
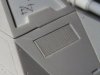
- Rear Nozzles: I used only the parts that close the end of these nozzles, and opened its ducts with a drill bit of the right caliber.
- Rear gun: I replaced its axis by another from turning aluminum to make it more strong.
• Pieces from scratch:
From the tip of the side canyons to the ends of the rear nozzles, all these important parts of the model have been made from scratch. The kit parts are so inaccurate that can't be used if it's to make a good replica of the original.
The vast majority of these pieces were previously planned and built in a free 3D application (Google SketchUp). Very useful to get the right shapes and measures, and then transfer them to the scale of the model to make it in plastic.
The most complicated areas were:
- The interior of the wells of the upper airbrakes. These pieces have a lot of fine detail and we must also make them fit perfectly inside the rear trapezoidal blocks.
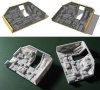
- The opening system of the upper airbrakes and the closing fit at the rear trapezoidal blocks. The axis of rotation is housed inside the rear nozzles, outside the trapezoidal block and had to take great care to close out as perfect as possible, so that they must be well integrated into the main part to hide that they are actually moving parts. The closure is so tight that I had to think and design a system to open them with no damage on the parts. The only way to open those airbrake is introducing a metal rod through the center hole of the rear nozzles to push its support piece and make it rotate on its axis. It works fine.
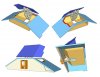
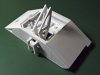
- The details on the front and rear sides of the front trapezoidal blocks. Again a lot of fine details, really small pieces and difficult to handle.
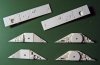
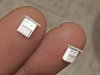
The cylindrical parts between the two trapezoidal blocks are built in layers or sections, always paying close attention to the center of each of these layers so that, to unite them all and form the final piece, were strung in a Ø1,6mm plastic rod. To make these different layers helped me a mini-drill and a mini-lathe. By working with these tools you ensure that all parts are concentric.
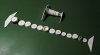
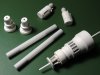
Finally, I pasted a few small pieces from the TIE Interceptor kit wings on the rear, just below the two nozzles, to simulate the details of the IL&M model.
PAINTING
The fuselage is painted with a mix of Tamiya acrylics: XF2 Matt White, XF19 Sky Grey and XF55 Deck Tan. Naturally, the proportions aren't fixed as they vary for each of the different colors showing each panel of the fuselage.
To paint each of the panels was necessary to make intensive use of masking tape to mask almost each of them separately.
Smooth filters and shadows were applied with airbrush using X19 Translucent Smoke.
The markings were painted with XF63 German Grey mixed with a bit of the fuselage color. Before painting those marks I distributed some specks of liquid mask to simulate the main chipping.
For some red signs I used the kit decals and some parts of the decals from the X-Wing kit. I also used decals drawn by computer and printed on virgin decal white paper to get the marks going in the back, on both sides of each nozzle, and on the right side of the vehicle, right next to the cockpit. These decals come in the kit, but the background color is yellow and not white. The areas where are located each one of the decals were first gloss varnished and then placed with the aid of Micro-Sol and Micro-Set products to minimize its thickness.
For other red signs and marks I found no valid decals, so I made masks and airbrush them using XF7 Matt Red, but reducing its intensity a little with the same mixture used for the fuselage. The more complicated markings were the lines that are on both sides of the model in the upper fuselage alongside the cannon tubes. To make them I had to plan the work so that were airbrush painted in three stages, painting a line on each side at every stage.
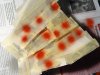
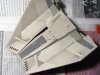
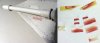
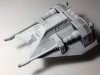
The small rectangular black marks that are scattered throughout the fuselage are made with transferable letters (Letraset type), using small dashes or sticks from the i letter.
The painting process is performed with major model subassemblies separately to work each group more comfortably. The junction areas of these pieces were previously masked for to keep the plastic clean in those areas and thus ensure that the glue works fine in the final assembly.
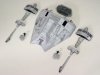
AGING AND EFFECTS
They are many and varied effects of aging and wear on these models. That's why they are so fun to paint. After making the overall paint job with great neatness, it is necessary to completely lose respect or fear of spoiling the model. You have to go for it (but with sense).
First we have to attack it with sharp and abrasive objects: We must do more or less intense dents everywhere, especially on the perimeter edge of the fuselage. We must also make chipping paint on many points. For these operations I used metal files, punches, blades ... etc.
These effects are completed drawing small patches of white with a very fine brush then profiling with medium gray to give more realism to the chipped paint effect. You can also do the reverse, painting gray spots and filling inside then with white. You can even use a hard lead pencil to make some of those profiles (see red circle). And it's also possible to invert the colors, leaving the central part in gray and the profile in white (See purple circle).
The spots, shadows and impacts are realized, when they are very blurred, with pastel colors, using black, white, gray, orange-rust, and brown tones. The color bar is passed on a piece of sandpaper and the powder obtained was applied to the model with the help of cotton sticks and smudger pen (see green circle). When they are more defined I prefer to use oil colors diluted in Humbrol enamels solvent and applied to brush tip (see orange circle). We can make multiple combinations of these techniques when deemed necessary (see brown circle: Pastel + acrylic white). The hard lead pencil is also a good tool to simulate the smaller bumps and scratches. Furthermore, the effect can be soften a little by rubbing with a cotton stick (see blue circle).
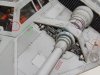
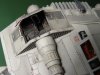
Then I darkened a bit all the panel lines with a mixture of black+brown oil colors very diluted, applied with a fine brush.
We also must torture our model by rubbing some zones with fine steel wool to create varied scratches and scuffs.
For example, the rear radiator is painted giving a thin layer of fuselage color directly over the metallic finish that had for 20 years. After drying, the piece was rubbed with fine steel wool on different areas, with the result that the acrylic layer was damaged, jumping from its base in small chippings and scratches. As the original metallic color was very dark, the chipping were too contrasted, so I apply a new thin layer of the same color as above to soften the contrast, and I went back to rubbing with steel wool, but with more care to create new small chippings and scratches. The result is very rich in nuances because the effects of the first rubbing are also appreciated, but more smoothed, and complement well with the effects created on the second rubbing.
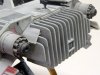
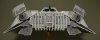
It's advisable to apply a overall thin coat of matt varnish between each phase of painting and aging to protect the work already done.
I also advise applying a topcoat before giving the model by finished.
I usually use the MicroScale water based varnish for the intermediate stages. And for the final sealing I use Marabu spray matt varnish. But I don't use the spray directly, rather I spray it first in a little glass pot until I get some liquid, and then I apply it with the airbrush, which makes a finer and reliable spray (the spray usually projects undesirable droplets). The finish with this varnish is very matt and tough, and airbrush is cleaned with Humbrol enamels solvent.
I present my new model. A work that began as a restoration project but, due to the poor state of my old model and the inaccuracy of the kit, finally became a construction project almost from scratch.
• Rescued Pieces:
I Rescued a few pieces of my old model (built in 1995) which was already spoiled by having been exhibited without protection for many years.
From that model I only rescued the cockpit with its pilots and the rear radiator.
The cockpit that I built is very rich in details regarding the kit piece, and the pilots are the pieces provided by the kit, but I remove their heads to leave empty helmets and filled these spaces with new and better modeled heads. I also put their corresponding goggles from a transparent yellow acetate sheet.
The only update after 20 years was to add a plastic strip in both helmets, in the relief that runs along the upper central line. The original relief of the pieces is very flat and needed more height to become more like the real helmets. Aside from that, I didn't need to re-touch up the paint job done so long ago. The cockpit had been well protected behind the glass of the windows.
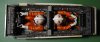
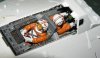
The rear radiator was also very well preserved because it had been painted with Humbrol polished metal, and not appreciated in its finish any alteration. This piece is the one that comes in the AMT/ERTL kit without any transformation or improvement.
• Parts from a new kit:
Almost all parts that I used from the new kit had to be worked to match the original model. The only parts that I used from de box are the supports of the lower airbrakes.
- Fuselage: First I removed completely all panel lines and details in relief, and then I go back to carving all the new lines and adding the small reliefs with different thicknesses plastic sheet.
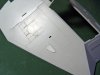
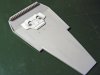
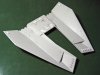
I cut the front grid into rectangle shape by the process of repeatedly passing the edge of a blade to make the cut as thin as possible. Once the rectangle was removed, I sanded the rest of the grid that remains in the main part of the fuselage until it disappears, leaving the front surface completely smooth. Then I pasted the rectangular piece in place, but leaving it a little swamped with respect to the surface that surrounds it.
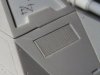
- Rear Nozzles: I used only the parts that close the end of these nozzles, and opened its ducts with a drill bit of the right caliber.
- Rear gun: I replaced its axis by another from turning aluminum to make it more strong.
• Pieces from scratch:
From the tip of the side canyons to the ends of the rear nozzles, all these important parts of the model have been made from scratch. The kit parts are so inaccurate that can't be used if it's to make a good replica of the original.
The vast majority of these pieces were previously planned and built in a free 3D application (Google SketchUp). Very useful to get the right shapes and measures, and then transfer them to the scale of the model to make it in plastic.
The most complicated areas were:
- The interior of the wells of the upper airbrakes. These pieces have a lot of fine detail and we must also make them fit perfectly inside the rear trapezoidal blocks.
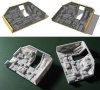
- The opening system of the upper airbrakes and the closing fit at the rear trapezoidal blocks. The axis of rotation is housed inside the rear nozzles, outside the trapezoidal block and had to take great care to close out as perfect as possible, so that they must be well integrated into the main part to hide that they are actually moving parts. The closure is so tight that I had to think and design a system to open them with no damage on the parts. The only way to open those airbrake is introducing a metal rod through the center hole of the rear nozzles to push its support piece and make it rotate on its axis. It works fine.
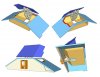
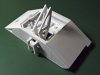
- The details on the front and rear sides of the front trapezoidal blocks. Again a lot of fine details, really small pieces and difficult to handle.
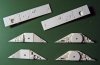
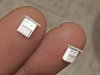
The cylindrical parts between the two trapezoidal blocks are built in layers or sections, always paying close attention to the center of each of these layers so that, to unite them all and form the final piece, were strung in a Ø1,6mm plastic rod. To make these different layers helped me a mini-drill and a mini-lathe. By working with these tools you ensure that all parts are concentric.
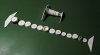
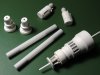
Finally, I pasted a few small pieces from the TIE Interceptor kit wings on the rear, just below the two nozzles, to simulate the details of the IL&M model.
PAINTING
The fuselage is painted with a mix of Tamiya acrylics: XF2 Matt White, XF19 Sky Grey and XF55 Deck Tan. Naturally, the proportions aren't fixed as they vary for each of the different colors showing each panel of the fuselage.
To paint each of the panels was necessary to make intensive use of masking tape to mask almost each of them separately.
Smooth filters and shadows were applied with airbrush using X19 Translucent Smoke.
The markings were painted with XF63 German Grey mixed with a bit of the fuselage color. Before painting those marks I distributed some specks of liquid mask to simulate the main chipping.
For some red signs I used the kit decals and some parts of the decals from the X-Wing kit. I also used decals drawn by computer and printed on virgin decal white paper to get the marks going in the back, on both sides of each nozzle, and on the right side of the vehicle, right next to the cockpit. These decals come in the kit, but the background color is yellow and not white. The areas where are located each one of the decals were first gloss varnished and then placed with the aid of Micro-Sol and Micro-Set products to minimize its thickness.
For other red signs and marks I found no valid decals, so I made masks and airbrush them using XF7 Matt Red, but reducing its intensity a little with the same mixture used for the fuselage. The more complicated markings were the lines that are on both sides of the model in the upper fuselage alongside the cannon tubes. To make them I had to plan the work so that were airbrush painted in three stages, painting a line on each side at every stage.
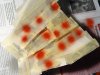
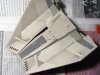
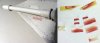
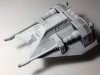
The small rectangular black marks that are scattered throughout the fuselage are made with transferable letters (Letraset type), using small dashes or sticks from the i letter.
The painting process is performed with major model subassemblies separately to work each group more comfortably. The junction areas of these pieces were previously masked for to keep the plastic clean in those areas and thus ensure that the glue works fine in the final assembly.
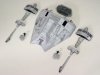
AGING AND EFFECTS
They are many and varied effects of aging and wear on these models. That's why they are so fun to paint. After making the overall paint job with great neatness, it is necessary to completely lose respect or fear of spoiling the model. You have to go for it (but with sense).
First we have to attack it with sharp and abrasive objects: We must do more or less intense dents everywhere, especially on the perimeter edge of the fuselage. We must also make chipping paint on many points. For these operations I used metal files, punches, blades ... etc.
These effects are completed drawing small patches of white with a very fine brush then profiling with medium gray to give more realism to the chipped paint effect. You can also do the reverse, painting gray spots and filling inside then with white. You can even use a hard lead pencil to make some of those profiles (see red circle). And it's also possible to invert the colors, leaving the central part in gray and the profile in white (See purple circle).
The spots, shadows and impacts are realized, when they are very blurred, with pastel colors, using black, white, gray, orange-rust, and brown tones. The color bar is passed on a piece of sandpaper and the powder obtained was applied to the model with the help of cotton sticks and smudger pen (see green circle). When they are more defined I prefer to use oil colors diluted in Humbrol enamels solvent and applied to brush tip (see orange circle). We can make multiple combinations of these techniques when deemed necessary (see brown circle: Pastel + acrylic white). The hard lead pencil is also a good tool to simulate the smaller bumps and scratches. Furthermore, the effect can be soften a little by rubbing with a cotton stick (see blue circle).
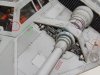
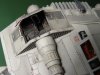
Then I darkened a bit all the panel lines with a mixture of black+brown oil colors very diluted, applied with a fine brush.
We also must torture our model by rubbing some zones with fine steel wool to create varied scratches and scuffs.
For example, the rear radiator is painted giving a thin layer of fuselage color directly over the metallic finish that had for 20 years. After drying, the piece was rubbed with fine steel wool on different areas, with the result that the acrylic layer was damaged, jumping from its base in small chippings and scratches. As the original metallic color was very dark, the chipping were too contrasted, so I apply a new thin layer of the same color as above to soften the contrast, and I went back to rubbing with steel wool, but with more care to create new small chippings and scratches. The result is very rich in nuances because the effects of the first rubbing are also appreciated, but more smoothed, and complement well with the effects created on the second rubbing.
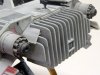
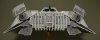
It's advisable to apply a overall thin coat of matt varnish between each phase of painting and aging to protect the work already done.
I also advise applying a topcoat before giving the model by finished.
I usually use the MicroScale water based varnish for the intermediate stages. And for the final sealing I use Marabu spray matt varnish. But I don't use the spray directly, rather I spray it first in a little glass pot until I get some liquid, and then I apply it with the airbrush, which makes a finer and reliable spray (the spray usually projects undesirable droplets). The finish with this varnish is very matt and tough, and airbrush is cleaned with Humbrol enamels solvent.
Last edited: