Dragon Age "Dagger" Project
So I have been lurking on the RPF for years now, helping folks when I might with a reply or a personal message, but largely I have kept quite and tried to learn as much as I can. I have, however, finally finished a piece in which I am somewhat proud. I have a few older projects I plan to put up, but I wanted to start with something good, but it does require some back story.
Quite a while back I helped a fellow forum member, daenarahd, who was looking to recreate a "dagger" from the Dragon Age universe. This was, if I remember, in the lead up to the launch of Dragon Age Inquisition. Being a fan of the franchise, I did my best to provide some design outlines of the blade in question. daenarahd provided most of the reference photos:

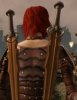
Apparently, in the Dragon Age world these things are considered "daggers." To keep the authenticity a bit, I judged the size from the character Leliana. I also looked up some details on the longest blades that can still be considered "daggers." I came up with a rather large 24 inches, which still doesn’t represent Leliana's proportions, but it keeps it closest to the extreme length of what human society might, very rarely, call a dagger - the thing is a sword, but whatever.
Anyways, I gave the designs back, hoping I would see the work show up here, as I was too busy at the time to invest in the creation of such a blade.
Designs:
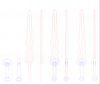
After a while, though, I went back to the project and decided I could take a crack at it. Using laser cut MDF I managed to create the blade and hilt. Sent out for the laser cutting mostly because I lost access to a real shop after moving to a place without a garage, so cutting MDF or any woodwork is not as feasible anymore. The lasers costs more, but the results are nice and symmetrical. The laser is also able to raster the blade and hilt designs. The blade was split, so I glued the two halves together and sanded the edging. The hilt was likewise put together for additional rounding and shaping with a hand sander and some sand paper. Spend a good couple of days trying to get the lines as close as I could to the original references. The pommel I 3d designed, largely because I wanted to get the flow between the hilt and pommel to match the whole design, and then printed this on my Afiania 3d printer - sadly this has recently broken down with a dead motherboard. Still, I learned a lot on that little thing. Got my sights on a Ultimaker 2 if I ever can save that kind of money. I have even started to redesigned the whole blade in 3d with those hopes in mind. I prefer using wood and a shop, but a 3d printer is still cheaper than adding a garage to the house.
I did not have a camera during much of the build, but I did manage to get the finish piece painted and all set up for a few "glamour" shots by borrowing a friend's I-phone for a camera.
Here are the results:
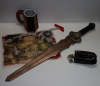
I cast three versions. One, pictured above, has a cold-cast bronze blade and an "iron" (metal powder and paint) hilt and pommel. The other two I have finished are both "steel" blades (cold cast aluminum) with bronze painted hilts and pommels. The Gems are cast clear with either pigment added or nail polish placed on the back for the color and simmer. The tang of the blade does not extend the full length of the hilt into the pommel, as this was outside my available length for MDF from the laser company. As such, the blade only goes part way through the hilt and is pinned in place with 1/16 inch steel rods. Hilt is wrapped with leather cord. One version has a suede flat wrap. Some of the blades are aged, others are not. The "iron" hilt I gave a strong aging, with rust and grime. Makes the bronze blade and gem really stand out.
Other pics:
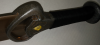
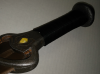
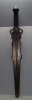
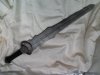
Last picture is from a bad phone camera, which is all I had until I borrowed my buddy's I-phone for the fancy shots. One day I will get a smart phone… or a real camera.
The blades were quite tricky to cast (one of the largest things I have solid cast thus far). I especially had some issues with the metal powders not always coating the whole mold or the resign (I used onyx) getting a bit too bubbly. The smooth on onyx is great for cold casting, but it is far more temperamental with humanity I think. Some of the blades have a slight "black" huge to areas were the powder was not thick enough or ran down as I poured the resin. It was a bit of a trick working alone. The blades tended to need quite a bit of cleanup, particularly the tips, were, despite my efforts, a few bubbles always seems to sit. I usually had to fill a few small holes with epoxy sculpt or filler, then paint with some matching colors or weather the area. The hilts, which I cast in three pieces, two halves of the hilt and the pommel separately, often needed internal cleanup to fill some holes. I was also never able to get a very clear "line up" on the two halves of the hilt after pulling the resin. They always seemed to flair out a bit more than the original. Probably my mold walls were not thick enough to fully support the mold full of resin, but I was working on some slim margins for the build, so it worked out better than I thought. Casting the 3d print required a bit more work, as even after lots of sanding and finishing, the silicone would still grab the smallest lines I could not even see on the original. Still, the paint hid quite a bit.
Any tips or suggestions would be great! I have one more cast set ready for assembly, with this last one have all cold cast parts (blade, hilt, pommel). I still have to clean up the hilt, but the pommel and blade are good to go.
So I have been lurking on the RPF for years now, helping folks when I might with a reply or a personal message, but largely I have kept quite and tried to learn as much as I can. I have, however, finally finished a piece in which I am somewhat proud. I have a few older projects I plan to put up, but I wanted to start with something good, but it does require some back story.
Quite a while back I helped a fellow forum member, daenarahd, who was looking to recreate a "dagger" from the Dragon Age universe. This was, if I remember, in the lead up to the launch of Dragon Age Inquisition. Being a fan of the franchise, I did my best to provide some design outlines of the blade in question. daenarahd provided most of the reference photos:

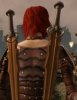
Apparently, in the Dragon Age world these things are considered "daggers." To keep the authenticity a bit, I judged the size from the character Leliana. I also looked up some details on the longest blades that can still be considered "daggers." I came up with a rather large 24 inches, which still doesn’t represent Leliana's proportions, but it keeps it closest to the extreme length of what human society might, very rarely, call a dagger - the thing is a sword, but whatever.
Anyways, I gave the designs back, hoping I would see the work show up here, as I was too busy at the time to invest in the creation of such a blade.
Designs:
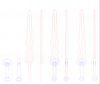
After a while, though, I went back to the project and decided I could take a crack at it. Using laser cut MDF I managed to create the blade and hilt. Sent out for the laser cutting mostly because I lost access to a real shop after moving to a place without a garage, so cutting MDF or any woodwork is not as feasible anymore. The lasers costs more, but the results are nice and symmetrical. The laser is also able to raster the blade and hilt designs. The blade was split, so I glued the two halves together and sanded the edging. The hilt was likewise put together for additional rounding and shaping with a hand sander and some sand paper. Spend a good couple of days trying to get the lines as close as I could to the original references. The pommel I 3d designed, largely because I wanted to get the flow between the hilt and pommel to match the whole design, and then printed this on my Afiania 3d printer - sadly this has recently broken down with a dead motherboard. Still, I learned a lot on that little thing. Got my sights on a Ultimaker 2 if I ever can save that kind of money. I have even started to redesigned the whole blade in 3d with those hopes in mind. I prefer using wood and a shop, but a 3d printer is still cheaper than adding a garage to the house.
I did not have a camera during much of the build, but I did manage to get the finish piece painted and all set up for a few "glamour" shots by borrowing a friend's I-phone for a camera.
Here are the results:
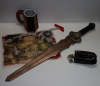
I cast three versions. One, pictured above, has a cold-cast bronze blade and an "iron" (metal powder and paint) hilt and pommel. The other two I have finished are both "steel" blades (cold cast aluminum) with bronze painted hilts and pommels. The Gems are cast clear with either pigment added or nail polish placed on the back for the color and simmer. The tang of the blade does not extend the full length of the hilt into the pommel, as this was outside my available length for MDF from the laser company. As such, the blade only goes part way through the hilt and is pinned in place with 1/16 inch steel rods. Hilt is wrapped with leather cord. One version has a suede flat wrap. Some of the blades are aged, others are not. The "iron" hilt I gave a strong aging, with rust and grime. Makes the bronze blade and gem really stand out.
Other pics:
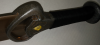
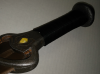
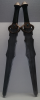
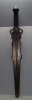
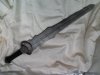
Last picture is from a bad phone camera, which is all I had until I borrowed my buddy's I-phone for the fancy shots. One day I will get a smart phone… or a real camera.
The blades were quite tricky to cast (one of the largest things I have solid cast thus far). I especially had some issues with the metal powders not always coating the whole mold or the resign (I used onyx) getting a bit too bubbly. The smooth on onyx is great for cold casting, but it is far more temperamental with humanity I think. Some of the blades have a slight "black" huge to areas were the powder was not thick enough or ran down as I poured the resin. It was a bit of a trick working alone. The blades tended to need quite a bit of cleanup, particularly the tips, were, despite my efforts, a few bubbles always seems to sit. I usually had to fill a few small holes with epoxy sculpt or filler, then paint with some matching colors or weather the area. The hilts, which I cast in three pieces, two halves of the hilt and the pommel separately, often needed internal cleanup to fill some holes. I was also never able to get a very clear "line up" on the two halves of the hilt after pulling the resin. They always seemed to flair out a bit more than the original. Probably my mold walls were not thick enough to fully support the mold full of resin, but I was working on some slim margins for the build, so it worked out better than I thought. Casting the 3d print required a bit more work, as even after lots of sanding and finishing, the silicone would still grab the smallest lines I could not even see on the original. Still, the paint hid quite a bit.
Any tips or suggestions would be great! I have one more cast set ready for assembly, with this last one have all cold cast parts (blade, hilt, pommel). I still have to clean up the hilt, but the pommel and blade are good to go.
Last edited by a moderator: