4505marcel
Active Member
Hey guys, I recently built a biker scout sniper rifle. I need some help with how to mold the thing as Ive never done anything like this before and want to produce some resin copies.
Now Ive watched some tutorials on you tube, so know roughly what im up against. With making a box, and half submerging it. Then making half the mold, flipping over, remove filler and pour the other half of the mold.
What Im stuck on is what exactly do I use to make the mold, bearing in mind Im UK based so that may help on where to buy. And also how to block the holes so the mold doesnt grab ect.
Hardest part is going to be the barrel I guess. I need something to use to block the main part, so I thought if I get a piece of unused box I can fill will resin and then push out to give me the internal form if you like. Making sure I leave it about 30mm longer each end to my barrel-
I then have an issue as I added a piece of tube ali to the top of my box to give it a better look, I was thinking I could cut anouther off cut and slip it inside my barrel in here-
Would it just be a case of getting some cley to seal the edges of my slots then?
The other issue is on my main reciever of the blaster, there is a recess where my barrel slips in, if the reciver is half filled and allowed to flow into the slot, when i do the other side and fill will it then be flexible enough to slip out of the slot once cured? The slot is about 60-70mm deep
Other parts are the muzzel break and scope but recon they are fairly easy to do, scope Im going to mold the scope mount clips attached
Now Ive watched some tutorials on you tube, so know roughly what im up against. With making a box, and half submerging it. Then making half the mold, flipping over, remove filler and pour the other half of the mold.
What Im stuck on is what exactly do I use to make the mold, bearing in mind Im UK based so that may help on where to buy. And also how to block the holes so the mold doesnt grab ect.
Hardest part is going to be the barrel I guess. I need something to use to block the main part, so I thought if I get a piece of unused box I can fill will resin and then push out to give me the internal form if you like. Making sure I leave it about 30mm longer each end to my barrel-
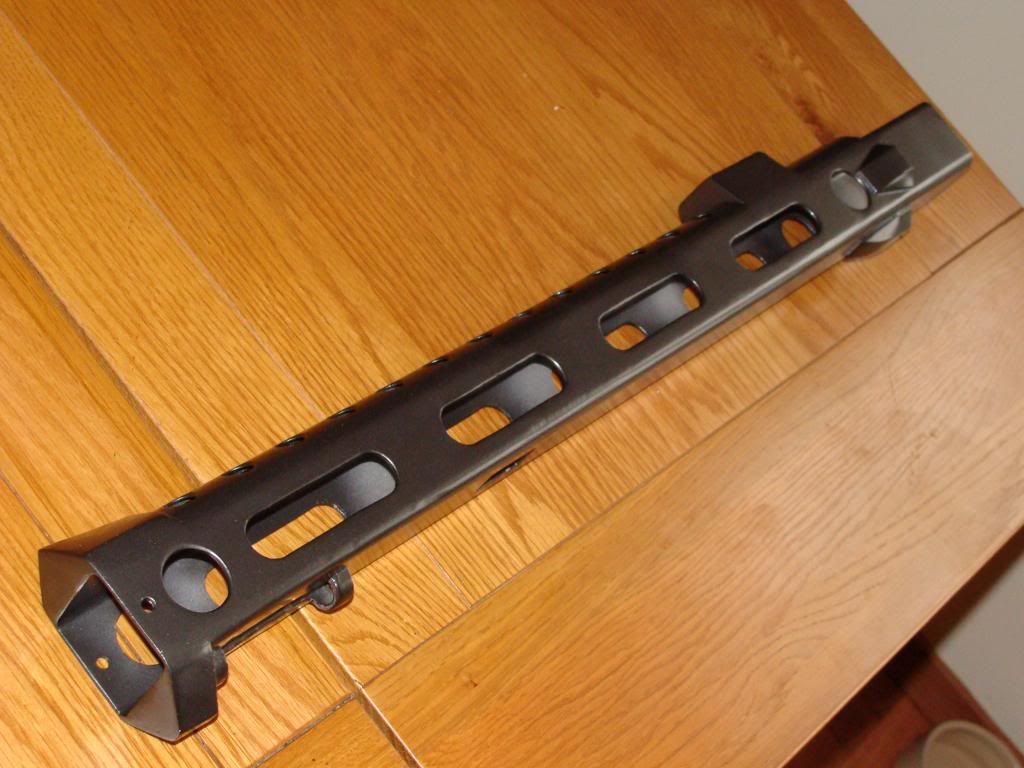
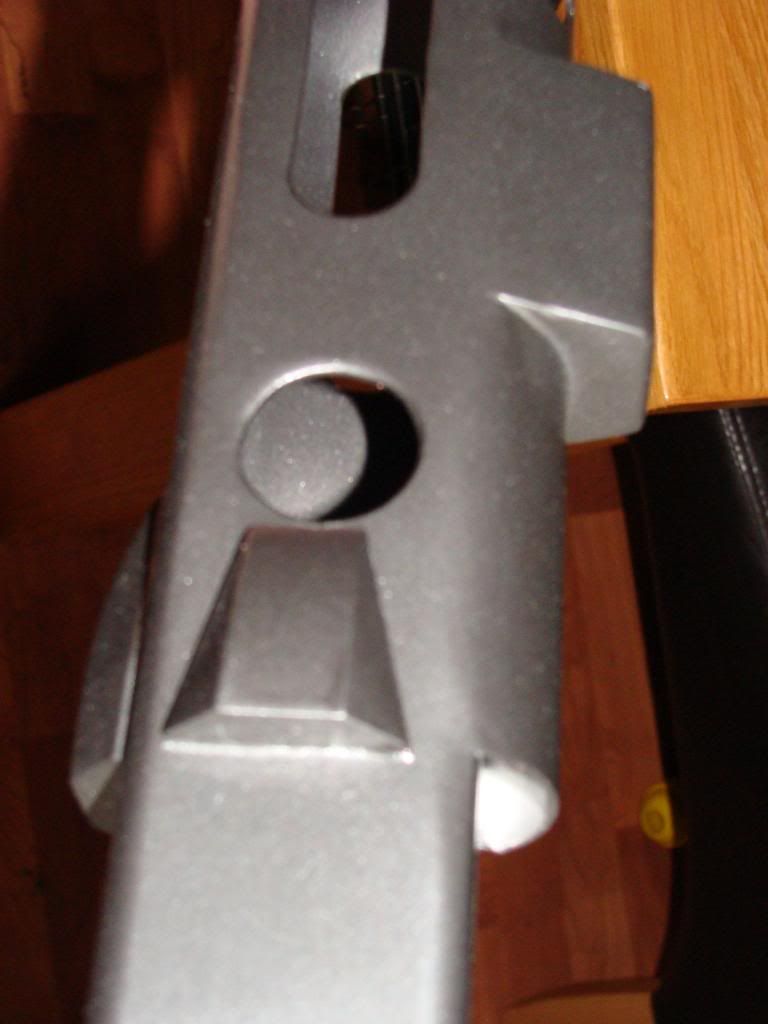
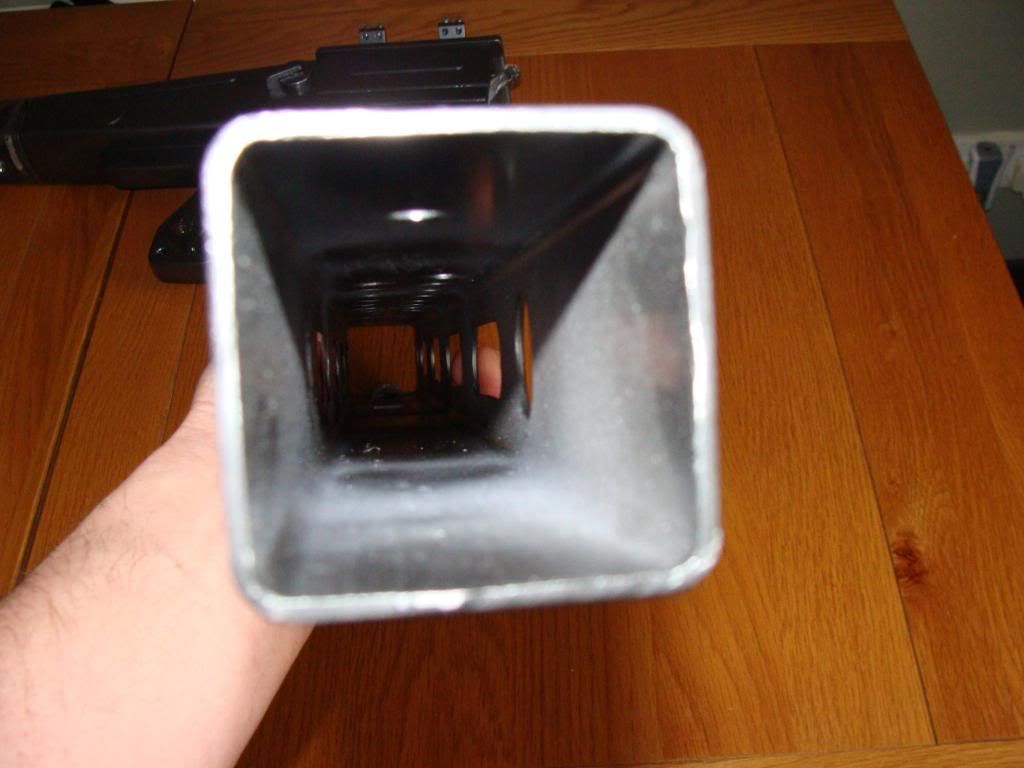
I then have an issue as I added a piece of tube ali to the top of my box to give it a better look, I was thinking I could cut anouther off cut and slip it inside my barrel in here-
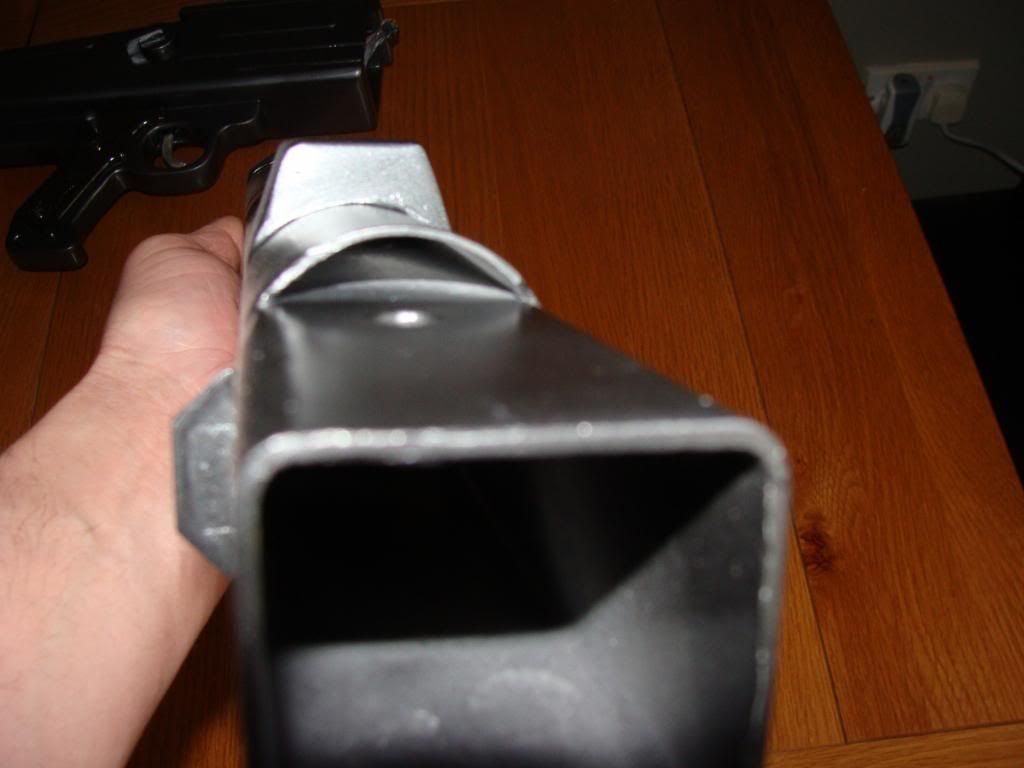
Would it just be a case of getting some cley to seal the edges of my slots then?
The other issue is on my main reciever of the blaster, there is a recess where my barrel slips in, if the reciver is half filled and allowed to flow into the slot, when i do the other side and fill will it then be flexible enough to slip out of the slot once cured? The slot is about 60-70mm deep
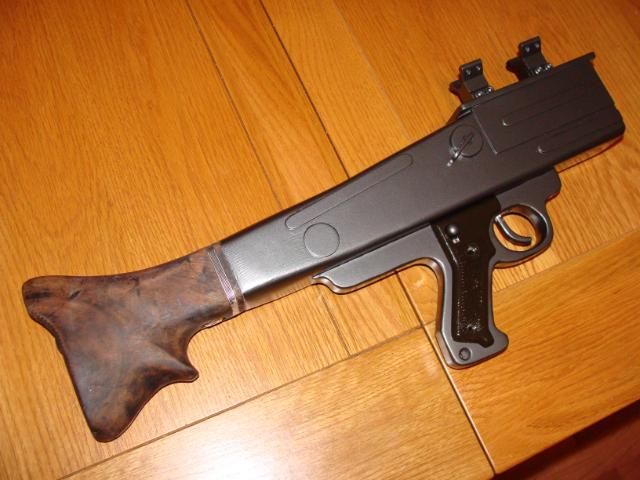
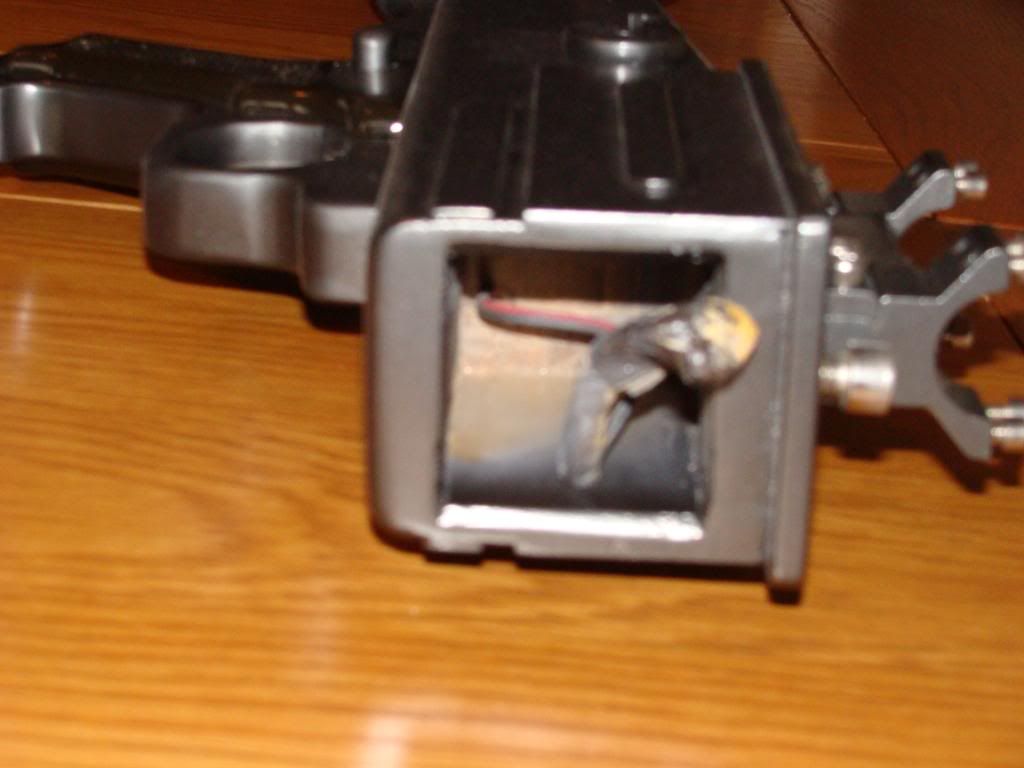
Other parts are the muzzel break and scope but recon they are fairly easy to do, scope Im going to mold the scope mount clips attached
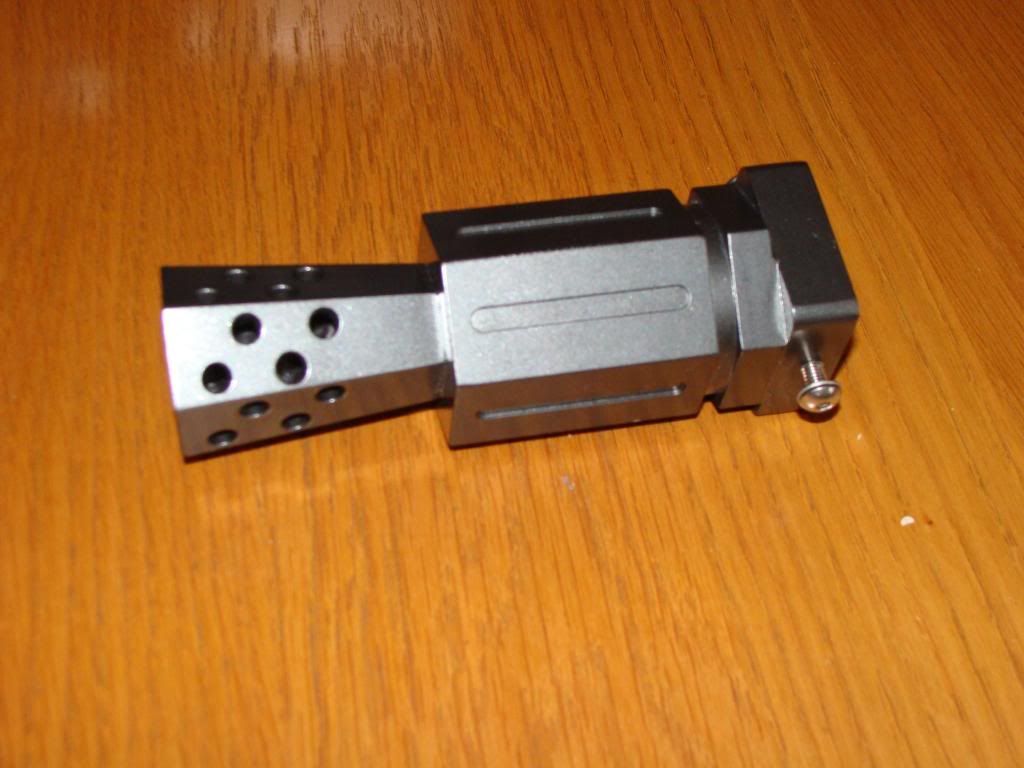
