Nazza84
New Member
Hello there! I've been always amazed by the work of the very talented community on this forum, and as MWiggs (he's making a fabulous, fantastic, amazing, wonderful armor: go see it!! http://www.therpf.com/showthread.php?t=239205) I've never thinked about making one myself before instantly falling in love for the SC2 marine armor assembled in the game trailer video; on a summer holiday I've seen Atelier Fantastic'Art making-of shootings for their SC2 armors (link: facebook album) and suddenly felt like I could go and try something similar, so I bought a polystirene box and tried to sculpt the thigh piece, wich is one of the less difficult pieces.
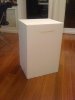
After some size calculations, with the cutting iron and the help of a projector I've managed to roughly cut the box to the size I need...
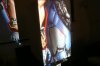
but the result were sooo baaaad. That was no good for my skills... Well, because I lack them! So I've put the project aside.
After some time I decided I'd try the pepakura way; this too, of course, was a new thing to me: so I've rushed and didn't read all that was to be read, didn't make or get a good 3D model, didn't manually unfold the model and got dozens of paper sheets lying around my floor.
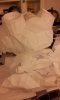
Of course I didn't read the part "NEVER USE STANDARD 85gr/squaremeter PAPER" wich is on every Pepakura guide, so after some hours of scissors and glue work everything looked like this:
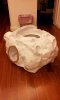
UGH.
Well, I was so enthusiast even with that result that next day I bought some heavier paper.
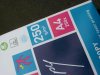
A LOTTA HEAVIER.
Well, this first post is getting longer than needed so let's skip some steps wich had me applying layers and layers of resin, from this...
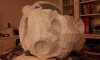
...to this.

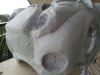
When I started using Dremel to cut details the whole thing started failing apart, so with much sorrow I throw it into our cellar, where it still stays. That last photo was from 2012. Foam forming? I wasn't so confident anymore on my skills so I didn't even try.
After a short time 3D printers were starting to get around the world, so I got interested in them; I had plans on using them for my build, but when the first multi-part prints I did had little bends on the side facing the build plate I started thinking about making a giant gantry. Yes, thermic retraction was the thing responsible for all the bends in the lowermost layers, and with huge prints could be an even bigger issue.
But I'm like a mad scientist so I don't care, I just go forth and try: that's why I've ended up making an ultra-low-cost 3D printer capable of nice detailing!
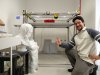
(that's me and some test prints made over the last months)
The gantry has a build volume of 1000x1000x1000 millimiters and solves the issue #1: lack of sculpting skills, my machine will do this for me!
(why this big? Torso piece! I don't know if I'll print it in one piece, but better be safe than sorry)
Anything, anyway, has pros and cons. PLA is cheap and doesn't warp that much, but is hard as hell to sand; weight is mostly what makes it not so good for this. I'll be looking for some lighter materials, so if any of you know of some lightweight filament please let me know! Of course not everything will be 3D printed, what comes out better in its real form (metal plates, bolts, screws, etc) will be used.
Any 3D printed part must be worked after print; syntered resin must make a UV light "bath", powder prints must be soaked into a hardening resin, ABS prints have the nice acetone vapor smoothing, PLA has nothing but sanding and priming with something like XTC3D (as far as I know). Given the size of what I was about to print, fused filament was the only available choice; cheaper and easier. Now that I got the printer, I had to make the models!
Now, just to let you know how mad someone can be: I've got near-zero skills on 3D modeling, but I've used Autodesk Inventor during university courses (I'm studying computer since, and for some years I've studied civil engineering. Let me give a huge thank you to Autodesk for offering students some licenses!), so I re-opened it and started drawing. Actually it makes working with joints a lot easier!
Let's say that in a couple days I've managed to develop this
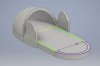
into this
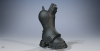
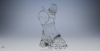
wich is actually made of 4 main parts: boot tip, boot heel, inner shoe, shin piece. I've started printing to get a feel of what it could be like walking in it and what I should modify:
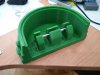
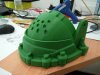
...and the weight popped up. Can't see from these photos, but 20% infill made a damn heavy boot (there's some serious uplift inside) unfortunately there is some wobbling on the Z-axis, I'll fix it later.
Here's a print job test just for the lulz:
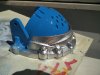
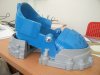
I've left some space to add all the short pipings later between inner shoe and heel.
Now I'm working on the thigh piece, up next will be the "hydraulic underwear" part but I'm researching the flexible pipes now, MWiggs found the perfect solution (thermal insulation pipes with a hose appearence, very flexible stuff) but I can't find anything similar here in Rome. Damn, I wish we had the hardware superstores I see in many Hollywood movies!

Hoping this time I won't fail, I salute you and will post again soon!
P.s. one last photo for the shin piece coming out of the printer right now:
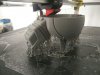
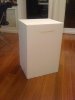
After some size calculations, with the cutting iron and the help of a projector I've managed to roughly cut the box to the size I need...
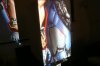
but the result were sooo baaaad. That was no good for my skills... Well, because I lack them! So I've put the project aside.
After some time I decided I'd try the pepakura way; this too, of course, was a new thing to me: so I've rushed and didn't read all that was to be read, didn't make or get a good 3D model, didn't manually unfold the model and got dozens of paper sheets lying around my floor.
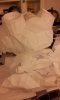
Of course I didn't read the part "NEVER USE STANDARD 85gr/squaremeter PAPER" wich is on every Pepakura guide, so after some hours of scissors and glue work everything looked like this:
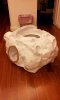
UGH.
Well, I was so enthusiast even with that result that next day I bought some heavier paper.
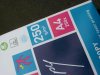
A LOTTA HEAVIER.
Well, this first post is getting longer than needed so let's skip some steps wich had me applying layers and layers of resin, from this...
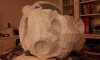
...to this.

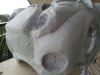
When I started using Dremel to cut details the whole thing started failing apart, so with much sorrow I throw it into our cellar, where it still stays. That last photo was from 2012. Foam forming? I wasn't so confident anymore on my skills so I didn't even try.
After a short time 3D printers were starting to get around the world, so I got interested in them; I had plans on using them for my build, but when the first multi-part prints I did had little bends on the side facing the build plate I started thinking about making a giant gantry. Yes, thermic retraction was the thing responsible for all the bends in the lowermost layers, and with huge prints could be an even bigger issue.
But I'm like a mad scientist so I don't care, I just go forth and try: that's why I've ended up making an ultra-low-cost 3D printer capable of nice detailing!
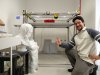
(that's me and some test prints made over the last months)
The gantry has a build volume of 1000x1000x1000 millimiters and solves the issue #1: lack of sculpting skills, my machine will do this for me!
(why this big? Torso piece! I don't know if I'll print it in one piece, but better be safe than sorry)
Anything, anyway, has pros and cons. PLA is cheap and doesn't warp that much, but is hard as hell to sand; weight is mostly what makes it not so good for this. I'll be looking for some lighter materials, so if any of you know of some lightweight filament please let me know! Of course not everything will be 3D printed, what comes out better in its real form (metal plates, bolts, screws, etc) will be used.
Any 3D printed part must be worked after print; syntered resin must make a UV light "bath", powder prints must be soaked into a hardening resin, ABS prints have the nice acetone vapor smoothing, PLA has nothing but sanding and priming with something like XTC3D (as far as I know). Given the size of what I was about to print, fused filament was the only available choice; cheaper and easier. Now that I got the printer, I had to make the models!
Now, just to let you know how mad someone can be: I've got near-zero skills on 3D modeling, but I've used Autodesk Inventor during university courses (I'm studying computer since, and for some years I've studied civil engineering. Let me give a huge thank you to Autodesk for offering students some licenses!), so I re-opened it and started drawing. Actually it makes working with joints a lot easier!
Let's say that in a couple days I've managed to develop this
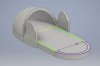
into this
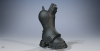
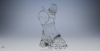
wich is actually made of 4 main parts: boot tip, boot heel, inner shoe, shin piece. I've started printing to get a feel of what it could be like walking in it and what I should modify:
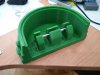
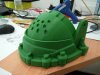
...and the weight popped up. Can't see from these photos, but 20% infill made a damn heavy boot (there's some serious uplift inside) unfortunately there is some wobbling on the Z-axis, I'll fix it later.
Here's a print job test just for the lulz:
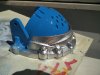
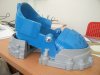
I've left some space to add all the short pipings later between inner shoe and heel.
Now I'm working on the thigh piece, up next will be the "hydraulic underwear" part but I'm researching the flexible pipes now, MWiggs found the perfect solution (thermal insulation pipes with a hose appearence, very flexible stuff) but I can't find anything similar here in Rome. Damn, I wish we had the hardware superstores I see in many Hollywood movies!

Hoping this time I won't fail, I salute you and will post again soon!
P.s. one last photo for the shin piece coming out of the printer right now:
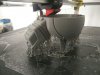
Last edited: