Vox
Sr Member
My friend wanted to be the Winter Soldier for Halloween this year, and commissioned me to build his arm. Rather than post as I went, I decided to just build the entire thing and post it all at once. The build process is below. Thanks for checking it out, and I hope you like it!
I started with two tape casts of his arm. The masking tape would be used to draw out patterns for the panels of the arm, while the duct tape would serve as the skeleton of the actual piece. This was done by wrapping the customer's arm in bubble wrap (to allow enough room for the piece to slide on and off), then in cling wrap (to allow for the tape to stick to something that could then be cut away), then finally tape.
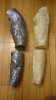
It takes a while to detail all of the panels on a piece like this, but using reference photos from the Captain America Civil War film, it was doable.
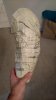
The next step was to cut apart the individual panels in the masking tape and transfer them to thin craft foam (like you might use for scrap booking). These panels would then be glued in place and together on the duct tape cast. Unfortunately though, the masking tape cast actually ended up slighly longer in circumference than the duct tape cast (likely due to the duct tape being harder to wrap around the arm, thus yielding a tighter cast). So all of the patterns I drafted had to be scrapped.
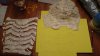
Rather than attempt another two casts and try to make them the same size, I used the duct tape casts as patterns to cut apart and trace onto thick stock paper. What you see here are the final drafts of those patterns, which have added cutouts/additions at the bottoms to allow for flexing of the elbow.
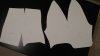
Here is the forearm portion, after it had been traced onto 1/4" foam and glued together using contact cement.
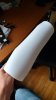
Once both pieces were glued together, I used a rotary tool to bevel the edges, giving them a smoother transition from the actual person's arm to the piece. Then each piece was treated with a heat gun. The heat gun makes the foam much more malleable, and you can bend and stretch and shape it to a shape, and it will hold that shape as it cool. Here, you can see how the piece looks far less angular than the previous photo, and has a few more contours of a natural human arm. The heat gun also serves to close the external cells of the foam, which allows for a smoother paint surface that won't absorb the paint when applied.
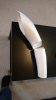
I needed to etch the panels of the arm into the foam, without cutting all the way through. I took a hobby knife and extended the blade only about 1/8", and set to work etching the details in the foam. This was a slow and meticulous process: I had no way to draw it out first and therefore had to be very careful. Once the patterns were all cut into the foam, I treated it with a heat gun again, which causes the edges of the patterns to curve inward just a bit, giving the piece more definition.
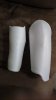
It was time to paint! Painting foam can be tricky because foam flexes, and any sort of acrylic or spray paint tends to crack and crease on a flexible surface. Thankfully there is leather paint, which is usually used for leather shoe customization, but works just fine for foam application as well. I coated the piece in straight black first, then applied several coats of the silver. The black underneath gave it a much more realistic tint, not to mention a slighly brushed/scuffed metal look.
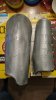
The patterns were not showing up as much as I wanted, so I thinned out some black paint and set to outlining and filling in the etches with a fine tip paint brush. As you can see, it definitely made a difference.
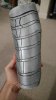
Thus, the finished product! I tore a sleeve from a thrift-store-purchased black track jacket, and just sewed around the opening to keep the accurate frayed look of the sleeve opening without allowing the jacket to continue unraveling. All the work was worth it to see the grin on his face when he wore it this Halloween.
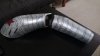
I started with two tape casts of his arm. The masking tape would be used to draw out patterns for the panels of the arm, while the duct tape would serve as the skeleton of the actual piece. This was done by wrapping the customer's arm in bubble wrap (to allow enough room for the piece to slide on and off), then in cling wrap (to allow for the tape to stick to something that could then be cut away), then finally tape.
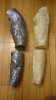
It takes a while to detail all of the panels on a piece like this, but using reference photos from the Captain America Civil War film, it was doable.
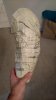
The next step was to cut apart the individual panels in the masking tape and transfer them to thin craft foam (like you might use for scrap booking). These panels would then be glued in place and together on the duct tape cast. Unfortunately though, the masking tape cast actually ended up slighly longer in circumference than the duct tape cast (likely due to the duct tape being harder to wrap around the arm, thus yielding a tighter cast). So all of the patterns I drafted had to be scrapped.
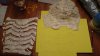
Rather than attempt another two casts and try to make them the same size, I used the duct tape casts as patterns to cut apart and trace onto thick stock paper. What you see here are the final drafts of those patterns, which have added cutouts/additions at the bottoms to allow for flexing of the elbow.
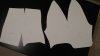
Here is the forearm portion, after it had been traced onto 1/4" foam and glued together using contact cement.
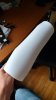
Once both pieces were glued together, I used a rotary tool to bevel the edges, giving them a smoother transition from the actual person's arm to the piece. Then each piece was treated with a heat gun. The heat gun makes the foam much more malleable, and you can bend and stretch and shape it to a shape, and it will hold that shape as it cool. Here, you can see how the piece looks far less angular than the previous photo, and has a few more contours of a natural human arm. The heat gun also serves to close the external cells of the foam, which allows for a smoother paint surface that won't absorb the paint when applied.
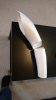
I needed to etch the panels of the arm into the foam, without cutting all the way through. I took a hobby knife and extended the blade only about 1/8", and set to work etching the details in the foam. This was a slow and meticulous process: I had no way to draw it out first and therefore had to be very careful. Once the patterns were all cut into the foam, I treated it with a heat gun again, which causes the edges of the patterns to curve inward just a bit, giving the piece more definition.
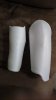
It was time to paint! Painting foam can be tricky because foam flexes, and any sort of acrylic or spray paint tends to crack and crease on a flexible surface. Thankfully there is leather paint, which is usually used for leather shoe customization, but works just fine for foam application as well. I coated the piece in straight black first, then applied several coats of the silver. The black underneath gave it a much more realistic tint, not to mention a slighly brushed/scuffed metal look.
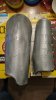
The patterns were not showing up as much as I wanted, so I thinned out some black paint and set to outlining and filling in the etches with a fine tip paint brush. As you can see, it definitely made a difference.
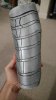
Thus, the finished product! I tore a sleeve from a thrift-store-purchased black track jacket, and just sewed around the opening to keep the accurate frayed look of the sleeve opening without allowing the jacket to continue unraveling. All the work was worth it to see the grin on his face when he wore it this Halloween.
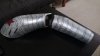