Silhouette
New Member
I've always been a bit intimidated to post here on the RPF, but over the last three years or so, costuming has become a huge thing for me, and Loki costumes my personal pet projects. I'm incredibly proud of the work and research I put into them, so I thought I could get over my lingering anxiety and, hey, show what I've done.
There are a loooot of WIP photos and steps, so I'm going to try to break it down. (Keep in mind this version is not yet complete at the time of this first posting, but it was wearable enough for a convention, heh.)
Technically, the Loki process started three years ago, and since then I've been updating and tweaking things; I remade the tunic about six months ago, and finally bullied myself into remaking the coat and armour over the past few months, as well, after realising how much my skills have improved since the first try.
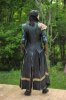
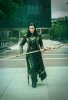
MATERIALS
My first costume was made from thin lambskin leather and a green linen-rayon blend from Joann Fabrics. It was nice, and it worked, but this time I wanted to really go for accuracy with the materials.
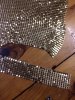
More to come!
There are a loooot of WIP photos and steps, so I'm going to try to break it down. (Keep in mind this version is not yet complete at the time of this first posting, but it was wearable enough for a convention, heh.)
Technically, the Loki process started three years ago, and since then I've been updating and tweaking things; I remade the tunic about six months ago, and finally bullied myself into remaking the coat and armour over the past few months, as well, after realising how much my skills have improved since the first try.
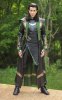
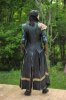
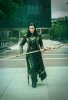
MATERIALS
My first costume was made from thin lambskin leather and a green linen-rayon blend from Joann Fabrics. It was nice, and it worked, but this time I wanted to really go for accuracy with the materials.
- black and brown goatskin leather, slightly thicker, that will hold up more
- veg-tan leather for the shoulders
- wool crepe, originally brown, and then hand-dyed about five times, for the green lining and accents
- black worbla for the armour pieces (sooo much nicer than regular worbla!)
- aluminum spider-mesh in gold for the coat-tail and armour accents
- about 10 gazillion zipper stops (actually well over 3,000 at this point; I still have to order more, ha!)
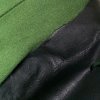
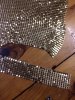
More to come!
Last edited by a moderator: