Re: Norbauer's Notebook - adventures in recreational Star Trek (mostly) prop replicat
Monday was largely an exercise in laser cutting;
Tuesday was an exercise in snow.
The Lasersaur cutter at the Artisan's Asylum has been down for some time, so on Monday I enlisted the generous help of Brian Johnson (the digital fabrication lab steward at the AA) in making a custom set of printer settings for the
Epilog Helix, in hopes that I could finally cut styrene. I prefer styrene to acrylic for scratch building because styrene is very easy to sand and weld. Unfortunately, acrylic is excellently laserable, styrene not so much. However, though took a couple of hours of fiddling around with tiny little two-second cuts of 1mm test squares, I'm happy to report that I was largely successful in finding some workable settings for styrene (detailed settings and information below), at least on the Epilog.
But first a bit of back story. I have been working with
Eric Ardros on a build of the the Subspace Beacon from TNG "Schisms."
This prop also appears in TNG "Cause and Effect" as a dekyon field modulator.
Thanks to Elvis's hand-drawn plans and my translating them into digital designs in Illustrator/CADtools, we had plans to make the planar components in styrene. (If anybody wants the plans to do this yourself, just PM me and I'll be happy to share.)
The many small curves and fine details of this design meant that cutting the design out by hand would be both tedious and tricky. It was thus the perfect project to try automated laser cutting.
However, having used the Epilog in the past, I knew that none of its existing materials settings would work. The best I could get it to do was to cut out some melted and charred out black figures that vaguely resembled my original design. And in the wrong size no less (more on this and Inkscape later).
However, Brian showed me how to create new materials settings for the Epilog and I began experimenting. The three relevant variables are:
- Vector Speed
- Vector Power
- Vector Frequency
My ultimate approach was systematically to titrate each variable independently and then to make a small test square cut after each change.
Even from the first few test cuts, some things became clear, the main one being that
low frequency is probably the most important strategy when it comes to lasering styrene. The concept here is very simple: the frequency controls the number of laser pulses per linear unit of travel of the focal point. A very low frequency would result in a perforated line, whereas a high-frequency line would be continuous. The advantage of low frequency on styrene is that it helps to avoid the material overheating. Lowering the power below anything close to what you would use on acrylic are also important steps toward the same end, but I found that the frequency decreased helped more than anything else and opened up room for me to start experimenting with power and speed (which had more to do with how many passes it took to cut rather than affecting the melting and flaming issues). Another important strategy is
multiple passes. You just have to get used to the idea that you're going to have to sit through many repetitive passes when working with styrene. The finer the details of what you're cutting, the lower the power you'll need to use and the more passes, sometimes up to 15 (!) in the case of very narrow walls <1-2mm. I found that too high a speed required far too many passes, so I ended up setting the speed surprisingly low as well as the power.
Here were the settings that worked best for me on 1.5mm styrene. (Interesting, the same held true for 2mm styrene; I just needed to make a few more passes.) Each number is on a scale out of 100.
Normal cutting
- power 15
- speed 15
- frequency 50
- 2 passes for score-and-snap, 4 passes for full cut-through
Fine detail cutting
- power 9
- speed 25
- frequency 60
- 15 passes, which should get you almost clear through the material
I found the 15 passes fine-detail cut particularly necessary for the part of the design
shown in this video. Those tiny little rounded rectangles have very narrow little filaments of dividers between them, which tended to snap as I was trying to snap out anything but a completely cut-through part. But on the normal power setting (which was already very low for styrene in the first place), these thin walls melted and deformed, while at the same fewer passes meant that the styrene wasn't cut through. With such fine details, trying to snap along scored lines just breaks everything at once, so you really need to cut almost all the way through (you can finish the job with a hobby knife if necessary if the 15 passes don't do the trick (or even do a few more passes, if you have more patience than I do!)
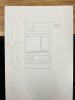
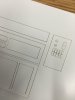
And here is the resulting build test-fit using electrical tape. (The buttons are 3M bumpons, SJ5008, if I remember correctly.)
Now, the problem is that all of the cuts are A LITTLE OFF. The culprit is Inkscape, which is the vector software that the Artisan's Asylum uses for printing to the laser cutter. Let me just say that, like most FOSS, Inkscape is an execrable piece of amateur-hour garbage, and anybody who says it's a plausible alternative to Illustrator for even the most trivial tasks has been dropping acid with Richard Stallman behind a bundle of CAT5 cables in a network wiring closet at MIT. No. No. No.
The issue is that Inkscape just silently throws away the dimensioning units from the files it imports (even when it's formats that accomodate them, such as PDF or AI) and converts everything to screen pixels using 90dpi as its assumption. Illustrator uses 72dpi (an admittedly archaic Adobe quasi-standard). However, in Illustrator's case this doesn't really matter because it actually understands real-world dimensions (dpi only comes into play with Pixel Preview or exporting to raster images), but Inkscape defaults to pixels for its native units (for
vector editing software?!). And so all of my drawings get scaled down at a 90:72 ratio, as best as I can tell. And I haven't been able to figure out how to scale them back up at the proper ratio thanks to Inkscape's counter-intuitive interface and horrible documentation. Yes, yes; I know Inkscape can theoretically import DXF, which allows you to set the units. However, that feature is totally broken and ignores half of my vectors. Ugh.
Sorry, I used to work in the open source world and I'm obviously still a little bitter about how ham-fisted most of its tools are.
I'm still searching for a workaround for the Inkscape scaling issue. An inspection of the relevant listservs isn't helping. I have a few ideas for workarounds:
- See about hooking my own Microsoft Surface up to the laser printer directly and printing to it from Illustrator (if the AA folks will let me and the drivers are available publicly)
- Try printing from a PDF viewer in Linux, which hopefully would respect the PDF format's native understanding of real-world units
- Try getting Inkscape to scale the artwork to compensate for its distortion factor
- Try figuring out if there is any export/import format that Inkscape will actually understand properly
Slowly but surely I'm figuring out this styrene pwpw thing though!