I know, this has been done, and done, and done again. But, nothing like doing something yourself, and I wanted something with a personal touch... so here we go with another!
This started as a project I wanted to do for my daughter, for Christmas, but with this year's Secret Santa, it was going to work great for my recipient as well. Why make one, when you can make two?!
There are a lot of 3D-printable models out there, so wasn't worth starting from scratch there. I found one I liked on Thingiverse, which would serve as a suitable base. The model had a design on one face, and wording already there on the other, as well as some other glyphs. I didn't want any of that, especially the wording, since "he" would be replaced with "she" in this instance. But, it was the only one I found which had a shaft for the handle, which went all the way through the head. This is important, because the final hammer would have some heft to it. It also had some handle pieces, but I didn't care to use those.
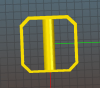
The hammer head was actually 4 separate pieces: main body, 2 end caps, and a round cap for the top.
Next decision was scale. I started out printing it at full scale, and ran into... issues. Stupid me, didn't ensure things were adhering properly, and I ran off for the weekend, while my printer did its thing. In this instance, however, its thing was an epic print fail.
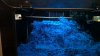
Following this disaster, I decided to scale things down to 50%. I started to worry about final weight, plus smaller was just going to be easier, given my time-frame.
I tried several prints with the main body laying on its side, but was never happy with the results; the angled sides were just too inconsistent, even with support. So, I tried flipping it on end, and that worked beautifully. After the final prints were ready for the body, and end caps, they were epoxied together with 1-minute epoxy.
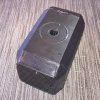
From here, the real work started.
This started as a project I wanted to do for my daughter, for Christmas, but with this year's Secret Santa, it was going to work great for my recipient as well. Why make one, when you can make two?!
There are a lot of 3D-printable models out there, so wasn't worth starting from scratch there. I found one I liked on Thingiverse, which would serve as a suitable base. The model had a design on one face, and wording already there on the other, as well as some other glyphs. I didn't want any of that, especially the wording, since "he" would be replaced with "she" in this instance. But, it was the only one I found which had a shaft for the handle, which went all the way through the head. This is important, because the final hammer would have some heft to it. It also had some handle pieces, but I didn't care to use those.
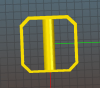
The hammer head was actually 4 separate pieces: main body, 2 end caps, and a round cap for the top.
Next decision was scale. I started out printing it at full scale, and ran into... issues. Stupid me, didn't ensure things were adhering properly, and I ran off for the weekend, while my printer did its thing. In this instance, however, its thing was an epic print fail.
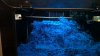
Following this disaster, I decided to scale things down to 50%. I started to worry about final weight, plus smaller was just going to be easier, given my time-frame.
I tried several prints with the main body laying on its side, but was never happy with the results; the angled sides were just too inconsistent, even with support. So, I tried flipping it on end, and that worked beautifully. After the final prints were ready for the body, and end caps, they were epoxied together with 1-minute epoxy.
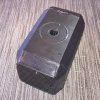
From here, the real work started.