Wednesday
Wednesday, I messed up a bit, and I didn't feel very much like posting on the forum afterwards.
But I do now.
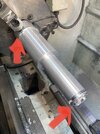
I made a mistake while cutting the thread, and the lathe is powerful and unyielding. So I had to sacrifice some length of the alu rod, and started over again. Fortunately, the diameter of the clamped bit was still way bigger than I needed it, so I was able to smooth it, and use it for clamping again.
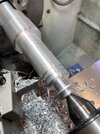
This time, the threading went well, and I made the disc and the thin bit, and then I began cutting the grooves. Since I didn't have a cutter with the right angle, I had to cut one half of each groove, then turn the tool sled to cut the other half of each groove.
Then, I realized that something about my calculated measurements for the groove depths wasn't right. They didn't turn out neither deep enough, nor wide enough. The distance from ridge to ridge was looking good, though.
Thursday
This morning, felt confident again, after the mess-up and the miscalculated grooves from yesterday. Right after waking up, the topic was back in my head, and I decided to mark all the ridges by scratching on both sides of each of them, and to then cut the angles to meet the marks.
Luckily, this time my plan worked.
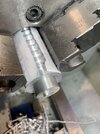
Then, I had to turn the part around, and reclamp it, wich was a bit nerve-racking, because the clamps have grooves, too.
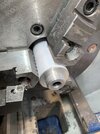
But it went well, and I was able to drill the bore, and to cut the thread.
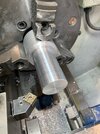
Next was the Graflex area of the hilt. I cut it down to a diameter a bit larger than the diameter of the grooved part, planed the front and drilled a center bore.
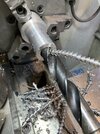
Then I drilled the big bore for another inner thread.
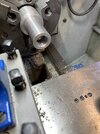
The last inner thread, I had drilled using a threat cutting drill, but today I cut my first inner thread using a lathe thread tool.
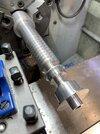
It worked, and I was treated another awesome moment when I assembled the saber as far as never before.
I'm quite happy with the result so far. Hopefully, the rest of the material will be long enough for the last two parts (remember, I need a bit more length for clamping, and for threads).
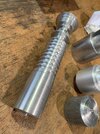
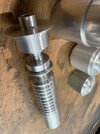